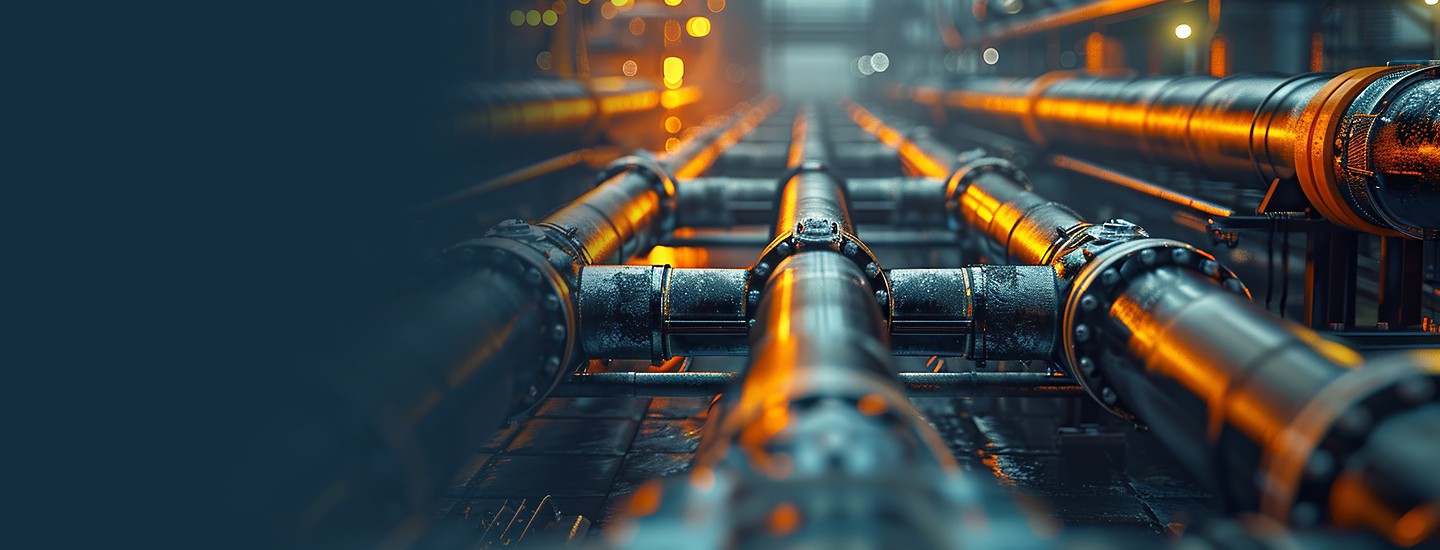
Article
6 questions for manufacturers to reduce sales tax overpayments
Manufacturers should ask these six questions to focus their sales and use tax strategy
Controlling spending is essential at a time when manufacturers are experiencing an unprecedented level of stress from many directions, including significant geopolitical disruptions. Given the amount of change recently, one important lesson learned this year is that many manual processes in sales and use tax departments are costly to the business and cannot be sustained. Although it might seem counterintuitive, this is exactly when you should be thinking about automating those manual processes to protect and future-proof your business. If you do, you’ll discover considerable value in better managing tax to optimize spend.
One way manufacturers can reduce spending is by improving controls on sales and use tax obligations. Because each manufacturer has tax complexities specific to their unique operations, there is no one-size-fits-all approach. However, there are implications of indirect taxes that all manufacturers need to address. These include overpayments of vendor-charged tax, potential penalties for underpaying tax, managing use tax accruals on inventory movements, and maintaining good relationships with suppliers.
Manufacturers are experiencing amplified sales and use tax complexities due to supply chain disruption
Escalating geopolitical tensions, such as the war in Ukraine and regional conflicts, have severely disrupted global supply chains, creating significant challenges for manufacturers worldwide. These disruptions are reshaping investment and sourcing strategies as manufacturers face altered supply routes and increased operational costs. This unstable environment causes a strategic reassessment of supply chain management to mitigate risks associated with geopolitical instability and maintain supply continuity.
In addition, these supply chain disruptions create a new challenge for manufacturers, making it more difficult to manage their sales and use tax obligations. Changes in manufacturing locations, supply chains, and trade lanes introduce new tax liabilities and compliance demands. Manufacturers need to respond quickly to these changes to handle the tax complexities of moving goods across borders and dealing with increasing procurement costs.
Save money by avoiding tax overpayments and controlling hidden and unnecessary spend
Manufacturing is changing rapidly. Your tax team must understand the indirect tax obligations and complexities resulting from purchasing decisions to facilitate changes in operations. While U.S. manufacturers don’t pay sales tax on raw materials used in a final product, they may be responsible for the indirect taxes on purchases of equipment and supplies such as machines, conveyor belts, and forklifts. Typically, these purchases are exempt from tax; the challenge is for companies to know whether the goods or equipment they are purchasing will be used in a manufacturing or research and development (R&D) process, which is usually tax exempt or reduced rate.
Your sales and use tax department must be confident that vendors are charging your business the proper tax because overpaying vendor-charged tax can add up quickly to significant amounts of money. If your vendor doesn’t charge the correct amount, your company is responsible for self-accruing taxes to ensure the correct tax is paid. While indirect tax overpayments can be costly, underpaying the vendor-charged tax can result in substantial penalties. These taxes can be very complex to track and manage, and the burden of accurate payments is on the manufacturer.
A related concern is that audit activity is increasing to make up for revenue shortfalls, and this primarily focuses on your procure-to-pay program. Even slight errors in purchasing can have an enormous financial impact. A small failure in a tax accrual process can turn a modest and necessary investment into tens of thousands of dollars in tax obligations. Other complexities arise from nexus rules and regulations, such as allocating an expense if the purchased item is used across multiple geographies — for example, if you buy software and use it at locations across numerous states. In some states, manufacturers get credits for R&D; other states have exemptions for manufacturing equipment. You need to know which regulations apply to your operations.
The point is that managing and tracking these various taxes requires your sales and use tax teams to understand the tax requirements for your industry in each tax jurisdiction where you and your suppliers operate — and these requirements change often. Manufacturers are finding this nearly impossible when relying on manual processes because they impose enormous demands on the tax teams’ time and energy and require a high level of specialized expertise. On the other hand, automated indirect tax software solutions can eliminate human errors, perform tasks more quickly and accurately, liberate your sales, and use tax teams to work more strategically and creatively.
Six questions to help you focus your manufacturing sales and use tax strategy
Assumptions can lead to unexpected and negative financial impacts. These assumptions can lead to errors that result in money being “left on the table.” A frank appraisal of your sales and use tax processes is a good place to start so that you can make the right decisions to improve efficiency and protect your business. These six questions can help you with that appraisal:
- Do you know if you’re overpaying vendor-charged tax on manufacturing equipment, raw materials, and other goods and services?
Some manufacturing companies have done reverse audits only to find they had overpaid taxes by hundreds of thousands and sometimes millions of dollars. Those overpayments are hidden costs and can be significant.
- Do you know how to calculate tax globally?
Many manufacturing suppliers get this wrong. As e-commerce and other digital channels rapidly gain adoption worldwide, suppliers suddenly have a global reach but don’t necessarily have global tax expertise.
- Do you know the potential consequences of inaccurately accruing use tax on inventory movements?
A company may often buy items into inventory without initially knowing how or where those things will be put to use. Once such items are moved and put into inventory, a second point in the transaction lifecycle is created when the tax team applies a tax analysis. It’s essential to have a tax accrual process in place to identify such transactions and calculate tax appropriately to minimize audit exposure.
- Would you know if your manufacturing company overpaid taxes?
If you pay too much and it is discovered, the government is under no obligation to tell you about it or refund that tax. It is up to you to prevent overpayments — and if you find any overpayments, it’s up to you to request a refund. Furthermore, if you rely on third-party consultants to manage this process, that is yet another additional cost due to not getting the tax right in the first place.
- Do you know what is subject to tax?
How a product or service is used can determine whether it is taxable. In addition, mixed-use items and items taken out of inventory for consumption — such as for free samples, internal use, or R&D — require tax calculation, which can be complex.
- How are you identifying manufacturing exemptions and tracking exemption certificates?
You can reduce the risk of penalties if you accurately identify and track tax-exempt purchases and exemption certificates — a complex process because the exemptions vary by tax jurisdiction. For example, some states have exemptions on products or services for R&D, some for manufacturing equipment, and so on. It’s important to ensure that your customers are supplying you with accurate exemption certificate information and you are exempting sales only when warranted.
Manufacturing companies face unpredictable tax challenges
Rapid changes in regulations and tax codes, the breakdown and restructuring of supply chains, and shifting market demands exacerbate the challenges manufacturers face. The Thomson Reuters 2023 Corporate Tax Departments Survey asked more than 300 tax managers and executives to reflect on the biggest challenges facing their teams. Respondents from close to one-half of businesses (47%) said they feel their tax department is under-resourced.
Many of these tax leaders understand that technology and automation can help them address some of their challenges. They realize that technology investments can have an immediate and dramatic impact on the bottom line and that automating procure-to-pay processes could prevent tax overpayments and save money.
For example, Lenovo, a global manufacturer of personal computers, aligned its tax strategies with business processes by automating and integrating its indirect tax processes with Thomson Reuters ONESOURCE Determination. This integration allowed Lenovo to overcome the logistic and geographic challenges of consolidating corporate tax processes globally and streamlining and integrating tax processes with its finance applications.
With a single software solution for U.S. and international transaction taxes, ONESOURCE Determination automatically calculates all tax rates and exemptions based on tax jurisdiction. For every requisition, purchase order, and AP invoice, our manufacturing sales and use tax software automatically calculates the tax value quickly and accurately the first time, eliminating time-consuming calculations and rework. For companies like Lenovo, this is essential to ensure that sales, use, and value-added taxes are calculated correctly in each of their locations around the globe.
As your business moves forward, don’t let sales and use tax issues cut into profits or keep you from creating distance between you and your competitors. Your organization may be overdue for genuine transformation — moving from manual to automated processes — and this may be the best time to make it happen. Let us help.
Avoid leaving money on the table from overpaid vendor-charged tax and protect your operational spend with ONESOURCE Determination.
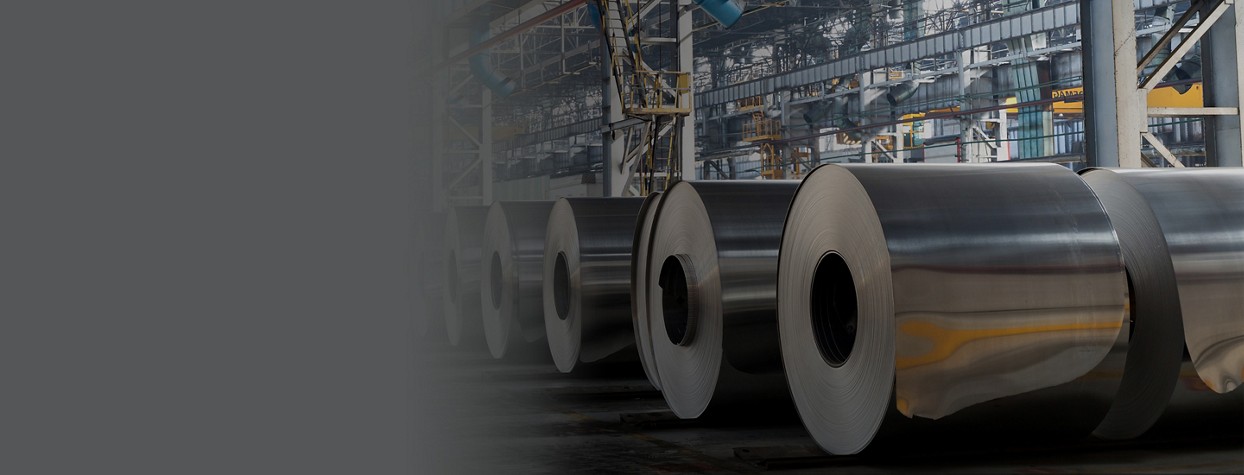
Manufacturing sales & use tax software
Automate your vendor-charged tax invoice reconciliation and decrease tax overpayments with procure-to-pay software